At the fourth consortium meeting, the current development progress and the achievement of the third milestone were discussed. This includes the completion of the development of the intelligent autonomous transport subsystem; the prototypes for interaction are available for further optimisation. The developed systems were also presented in the development halls of ELROTEC. The discussion of the development progress focused on the sensory exoskeleton, the intelligent autonomous transport system, human-technology interaction, gamification and training possibilities, as well as laboratory and field tests.
Regarding the sensory exoskeleton, activity recognition has been developed and the sensors were placed into the exoskeleton. In addition, the Elastomer switch function has been developed and implemented into the exoskeleton to enable activation and deactivation of the exoskeleton support; furthermore, a load cell was implemented to measure pressure and relief. RTT localisation has been integrated into ComFlow.
The implementation of the autonomous transport system’s integrated lifting unit with a load cell was successfull; the height of the lifting table can be can be adjusted individually for each employee to provide ergonomic relief during the commission and delivery of components. In addition, mobile load carriers have been developed. All functions of the autonomous transport system can be controlled via the ComFlow control framework.
On the topic of human-technology interaction, further discussion centered on the development of Smartwatch interaction functions, which control the lifting table of the autonomous transport system and activate the Follow-Me mode. Gesture-based control for interaction with the autonomous transport system has been further developed to enable controls of the lifting table. This new function has been presented together with the optimised Follow-Me mode.
Regarding the gamification and training measures, the gamification smartphone was optimised and presented. Various sensors can be connected to evaluate ergonomics. Team-functions and trophies were developed and added to the app; furthermore, the smartphone app was expanded to include employee profiles. Additionally, training documents were expanded.
On the topic of laboratory and field tests, the discussion centered on the successful lab testing of the expansion of the defined assembly process to include lifting table control. The defined commission process (including the lifting table control) and the Follow-Me mode were implemented and successfully tested in the laboratory; further tests were designed to evaluate the entire system.
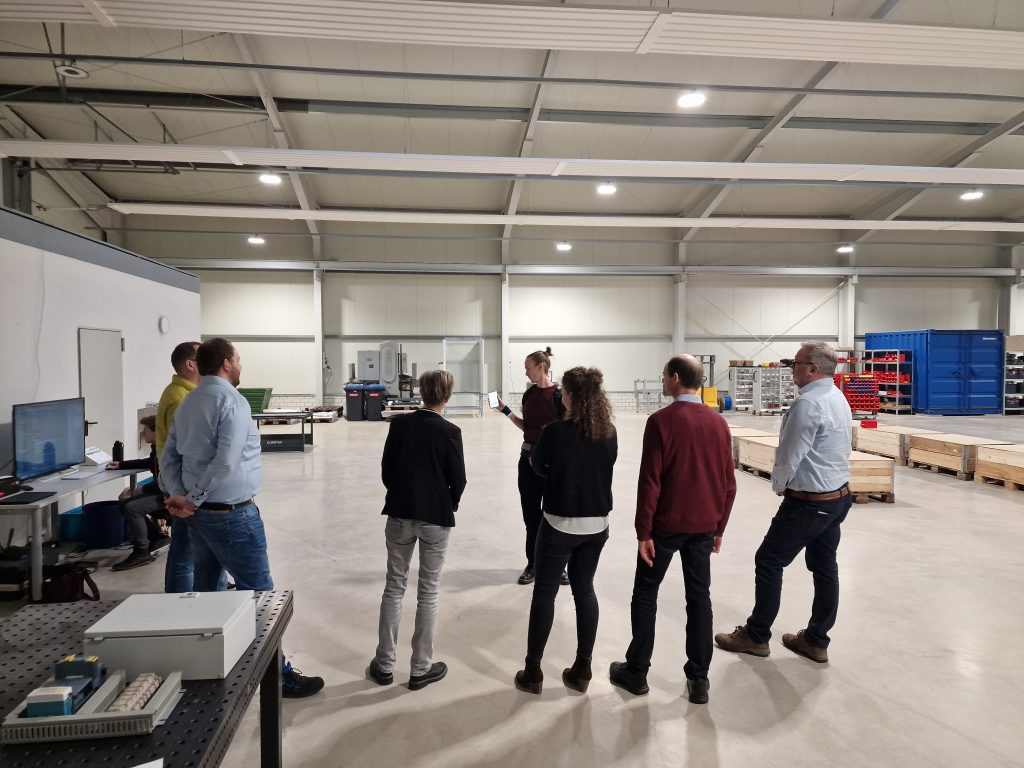